Induction Units With Medium-Frequency Technology
- Cost savings thanks to high efficiency
- Increased productivity thanks to shorter heating times
- Covers a wide range of mounting and dismounting applications
- Process reliability thanks to safe heating
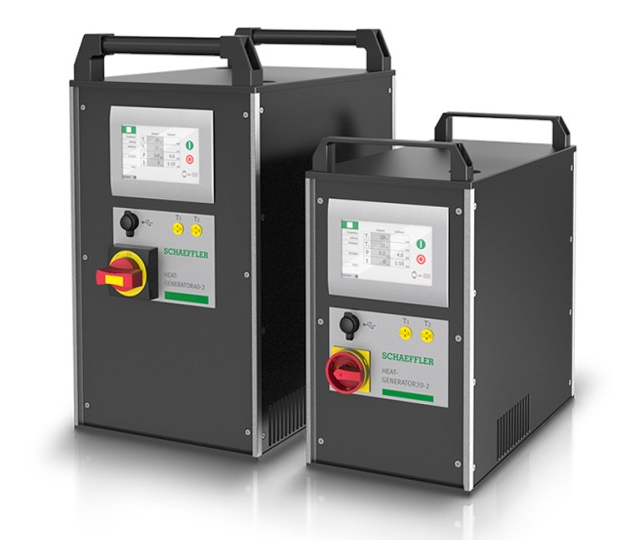
Unlike induction heating devices, induction units with medium-frequency technology are not only suitable for thermal mounting but also for removal. They can also be used to heat up very large and heavy components.
Adequate expansion of the bearings is achieved in most cases at +80 °C to +100 °C. During the heating process, the maximum heating temperature must be observed. To prevent changes to the structure and hardness of the bearing, the temperature of rolling bearings must not normally exceed +120 °C. In all devices for heating, the temperature can be controlled with continuous variability.
These units can likewise be used in mobile applications thanks to their high level of flexibility and compact design. It can therefore be used, for example, at construction sites for wind turbines or for other large components that are difficult to transport.
Each unit comprises a generator and inductor that is positioned on the workpiece. A rigid or flexible inductor is used, depending on requirements. Flexible inductors can be fitted in the bore or on the outside diameter of the workpiece, depending on the application in question. Flexible inductors are suitable for heating bearing inner rings and large components such as machine supports in wind turbines. The length of the inductor is determined in relation to the dimensions of the workpiece.
Rigid inductors are particularly well suited to volume production. Flexibility is less of a priority here than short setup times and a high level of process reliability.
Heating devices with medium-frequency technology have the following advantages:
- Suitable for mounting
- Suitable for dismounting
- Operating frequency from 10 kHz to 25 kHz
- Efficiency of the generator greater than 90%
- Low energy requirements
- Short heating times
- Time and temperature-based control as well as additional operating modes
- Automatic demagnetization
- Flexible and rigid inductors can be used
- Inductors can be used on either the inside or outside of the component
- Lower mains connection power than heating devices with mains frequency
- Almost silent
- Air-cooled system
Comprehensive reasons to use HEAT GENERATOR devices
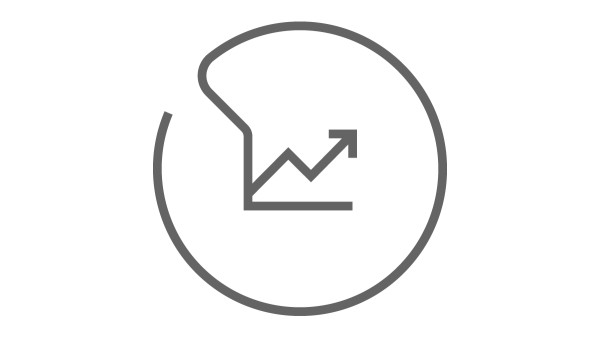
Higher efficiency
HEAT GENERATOR devices allow energy costs to be significantly reduced. With an efficiency level of >90%, the HEAT GENERATOR operates with a significantly higher level of energy efficiency than conventional heating devices.
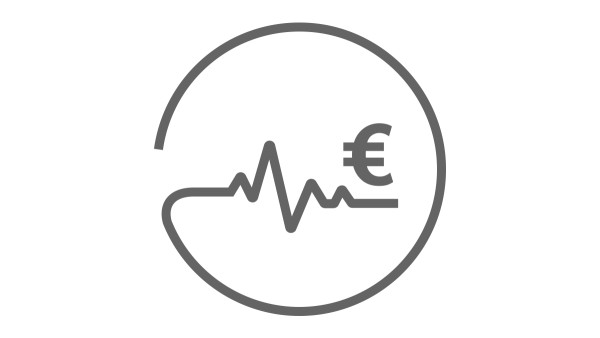
More productivity
The HEAT GENERATOR devices heat components faster than mains frequency devices, which increases productivity.
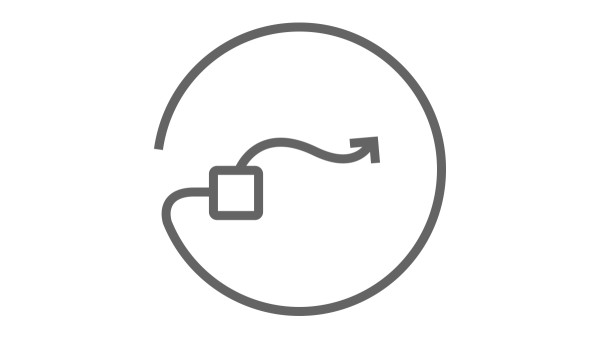
More flexibility
The HEAT GENERATOR is significantly more compact and almost 40% lighter than the previous generation. This makes the units mobile and suitable even for use in hard-to-reach areas. Depending on the application, mounting and dismounting work can be carried out using flexible or rigid inductors.
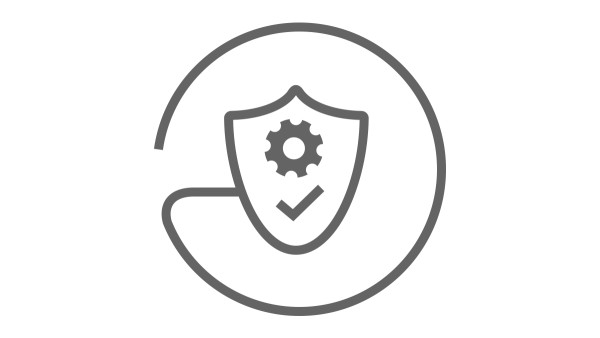
Enhanced reliability
The temperature control allows easy and reliable handling and prevents the workpiece overheating.
Features
- For large and heavy workpieces
- Digital control system
- Controlled via touch panel
- Comprises a generator and an inductor that can be either rigid or flexible.
- Rigid inductors are:
- Manufactured specifically for the application
- Light and can be easily placed on the workpiece
- Particularly suitable for the dismounting of bearing rings, labyrinth rings, and axlebox bearings in volume production
- Flexible inductors are:
- Similar to a cable, which can be attached to the bore or placed on the outside of the workpiece
- Up to 40 meters long, depending on the application
- Uniquely adaptable to different workpieces and suitable for particularly large bearings, gears, housings, etc.
- Rigid inductors are: